当社の強み
板厚12mmのS45Cをプレスで打ち抜き加工します
強み① 板厚12mmをプレスで抜き加工します
強み② 月産200万ショットの量産体制
強み③ ジグザグフィーダでコストダウン
強み④ パンチ・ダイ入れ替え方式で金型費用が安価
厚板プレス抜き加工のメリット
・切削加工に比べて材料のロスが少なく安価に加工できる
・レーザーやプラズマなどに比べて安価に大量に加工できる
・リロール材を使用すれば、板厚制度が向上でき、研磨工程を削減できる。
・丸棒切断よりも、鍛造工程後の穴ケア加工などの2次工程を削減できる ・バレル研磨やメッキなどの後工程にもご対応致します。
SCM435 100×50×12
「加工能力」
・最大サイズΦ200程度、最大板厚12mmまで加工できます
(板厚1~12mmまで対応できますが、6mm以上が得意です)
・月産200万パンチの生産能力
・500tプレス、150tプレスでレベラフィードで自動加工
「対応材種」
・普通鋼:SS400、SM590、SPCC、SPHCなど
・特殊鋼:S45C、SCM435、SK85、SKH51、SKD11など
※特殊鋼の取り扱いが70%以上です
※最大で500tプレスを保有し、各プレス機械に厚板の抜き加工に対応したダイセットを装備。金型も内製化し、金型にも独自のノウハウがあります。
①板厚12mmをプレス抜き加工します
S45C、SCM435、SK85、SKH51、SKD11などの特殊鋼のプレス抜き加工が得意です!
普通鋼は炭素(C)・ケイ素(Si)・マンガン(Mn)・リン(P)・硫黄(S)の鉄の5元素が含まれる鋼材でSS400やSPHCなどのSS材、SP材が代表的な材料です。汎用的な材料で幅広い用途に使用されています。熱処理はせず、素材のままやメッキや塗装をして使用します。
特殊鋼は、5元素にクロム(Cr)・ニッケル(Ni)・モリブデン(Mo)などの元素を添加することにより、高い強度、耐熱性、耐食性を付与することができます。特殊鋼は厳しい条件下での使用や、普通鋼よりも高性能が要求される部品に広く使用され、熱処理をしてさらに強度を高めることができます。
特殊鋼は熱処理が必要ではありますが、SC材の代表的な鋼種であるS45Cなどは熱処理性を保証している材料ではないので、選定の際には注意が必要です。
特殊鋼は普通鋼に比べて硬い材質ですので、一般的にはプレス加工には不向きですので、金型に独自の工夫が必要になります。
プレス抜き加工が可能な特殊鋼の例
名称 | 鋼種 | 用途 |
構造用炭素鋼鋼材(SC材) | S45C、SCM435など | ボルト・自転車のフレーム |
炭素工具鋼鋼材(SK材) | SK85など | 刃物・プレス金型 |
高速度工具鋼鋼材(SKH材) | SKH51、SKD11など | 鍛造金型・切削工具 |
プレス抜き加工が可能な普通鋼の例
名称 | 鋼種 | 用途 |
一般構造用圧延鋼材(SS材) | SS400など | 橋梁・船舶 |
溶接構造用圧延鋼材(SM材) | SM590など | 橋梁・船舶 |
冷間圧延鋼材(SPC材) | SPCCなど | 外装品・カバー |
熱間圧延鋼板(SPC材) | SPHCなど | 電気機器カバー |
上記の材料の中でも弊社は、S45C、SCM435などの(SC材)、SK85なども(SK材)などの特殊鋼を専門に取り扱う材料商社との仕入れ体制を構築しておりますので、コイル材・シート材を問わず幅広い供給体制があります。また、鋼種や板厚によっては保有在庫もございます。
②月産200万ショット量産体制
月産200万パンチの生産能力!
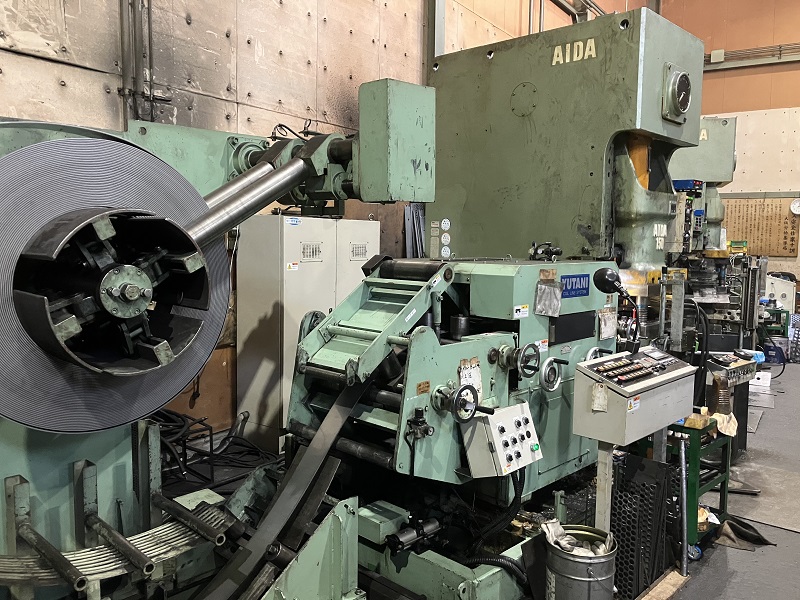
弊社ではメインプレスラインを500tプレス(自動・単発)1機、150tプレス(自動)2機にて量産加工体制を敷いております。板厚0.8mm~10mmまで、材料巾250mmまでレベラーフィードで対応可能です。
自動化することにより、材料歩留りの向上、生産効率のUP、不良率の減少などのメリットが見込まれます。
1ロットの生産数量は増加することになりますが、総合的に判断をすると費用対効果が見込まれます。
当社ではメインラインを自動化することにより、生産条件にもよりますが、少人数での操業や無人での操業も実現しており、高い生産性を実現しております。
・生産能力
500tプレス 50万パンチ/月
150tプレス 160万パンチ/月(2機合計) 150tプレス自動ライン
コイル材での材料供給が難しいような生産ロットや、試作対応、t12mmなどレベラーでの対応ができない場合はシート材でも対応しております。
③ジグザグフィーダでコストダウン
順送りフィーダとジグザグフィーダの比較
・順送りフィーダで15枚 生産した場合 |
・ジグザグフィーダで15枚 生産した場合 |
![]() |
|
材料巾を細くでき、材料ロスも少なくできる
通常の順送りレベラーフィーダで1列送りにすると、形状により歩留まりに限界がありますが、当社ではジグザグフィーダで多列抜きにすることで最大7%の歩留まりの向上が見込まれます。
また、当社のジグザグレベラーフィーダでは最大で250巾、7列抜きで加工できることで、1列で抜き加工をするよりも加工時間が長くなり、材料の交換にかかる時間を省略することができ、わずかですが歩留りも向上することになります。
細巾の材料を使用するとコイルが倒れやすくなりますが、当社のように多列で抜き加工をすると太巾の材料を使用することができ、作業の安全性も担保しやすくなります。
④パンチ・ダイ入れ替え方式で金型費用が安価
入れ替えパンチ・ダイ
プレス金型は通常ダイセットから制作するが
当社はパンチ・ダイのみで製作するので安価格
当社ではコンパウンド(総抜き)金型にてプレス抜き加工に対応しております。
通常のプレス金型であれば製品を立ち上げる際の金型費用として、ダイセットと呼ばれるプレス金型全体を考えますが、当社のコンパウド金型はダイセットをプレス機に据付したままで、パンチ・ダイのみを製作するだけになりますので、イニシャルコストで有利になります。また、パンチ・ダイのみを交換するだけなので、金型交換も短時間で行えますので、他の加工方法からプレス加工の検討の際には少ないコストでリスクを低減でき、サイズ違いの同様製品も併せて加工検討もしやすくなります。
コンパウンド金型は製品のノックアウト機構により金型内で板押え効果もありますので、送り抜き金型に比べ、平坦度が高いので、修正の平面押し加工を省略でき、バリやプレスだれが同一方向になるメリットもあります。
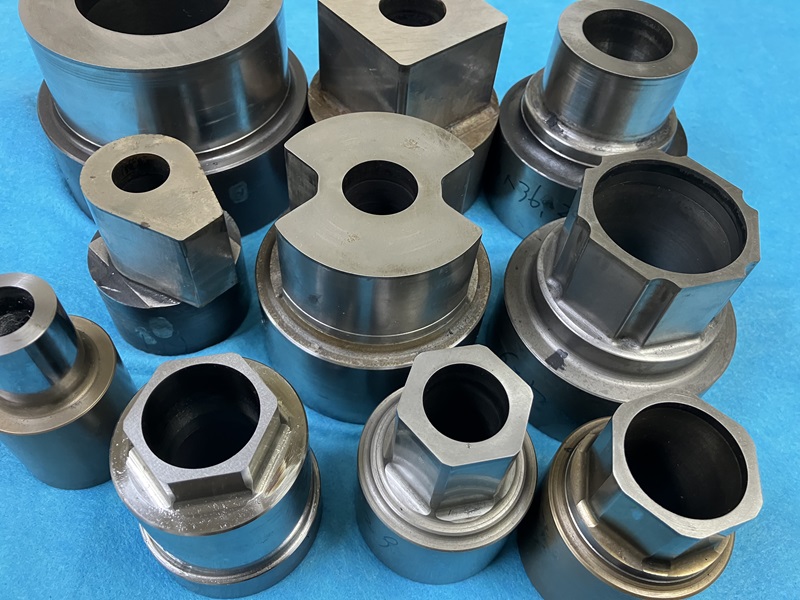